|
Post by Markbo on Jun 24, 2016 17:26:33 GMT -5
"....I could easily get 2400fps with the 750gr barnes and Woodleigh bullets..." Damn that hurts just reading it! 
|
|
|
Post by Lee Martin on Aug 1, 2016 19:45:06 GMT -5
I finally got serious about building this Nyati. Sunday test threads were cut on scrap chrome moly to ensure we can time 2mm’s to the receiver. As earlier noted, CZ main rings are metric. Normally we chamber on my dad’s Harrison or a South Bend Heavy 10 at my house. Those only do standard threads however. Our big 15” Nordic handles both. This is one of our larger lathes and with a 10 horsepower motor it makes chips fast. 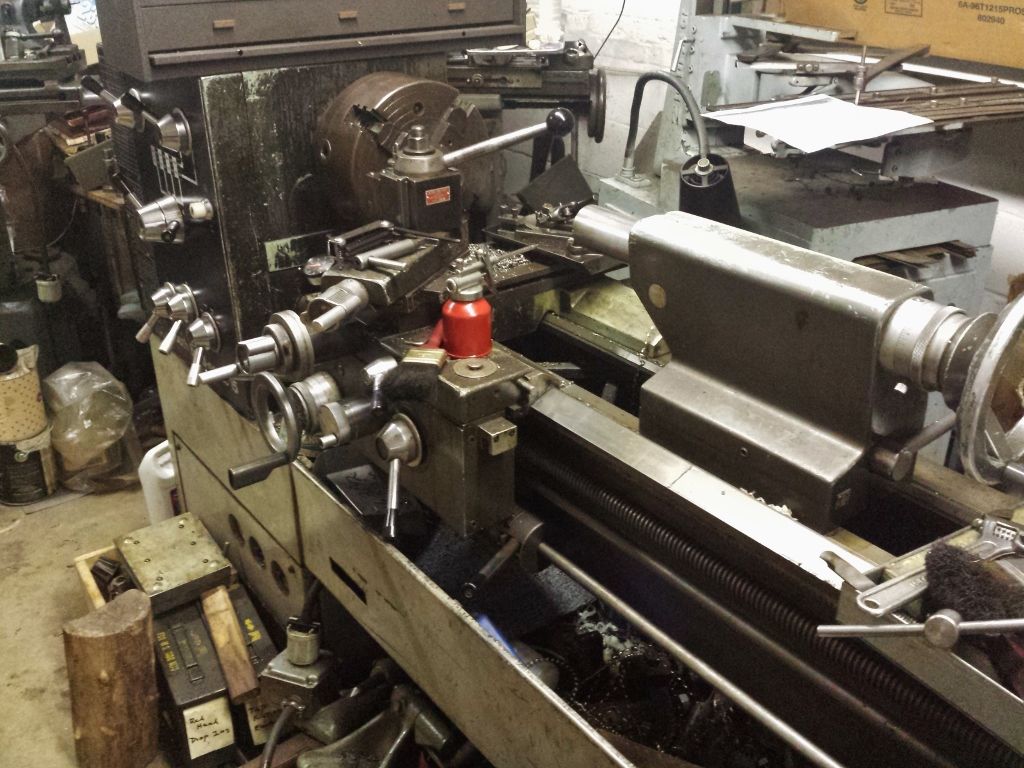 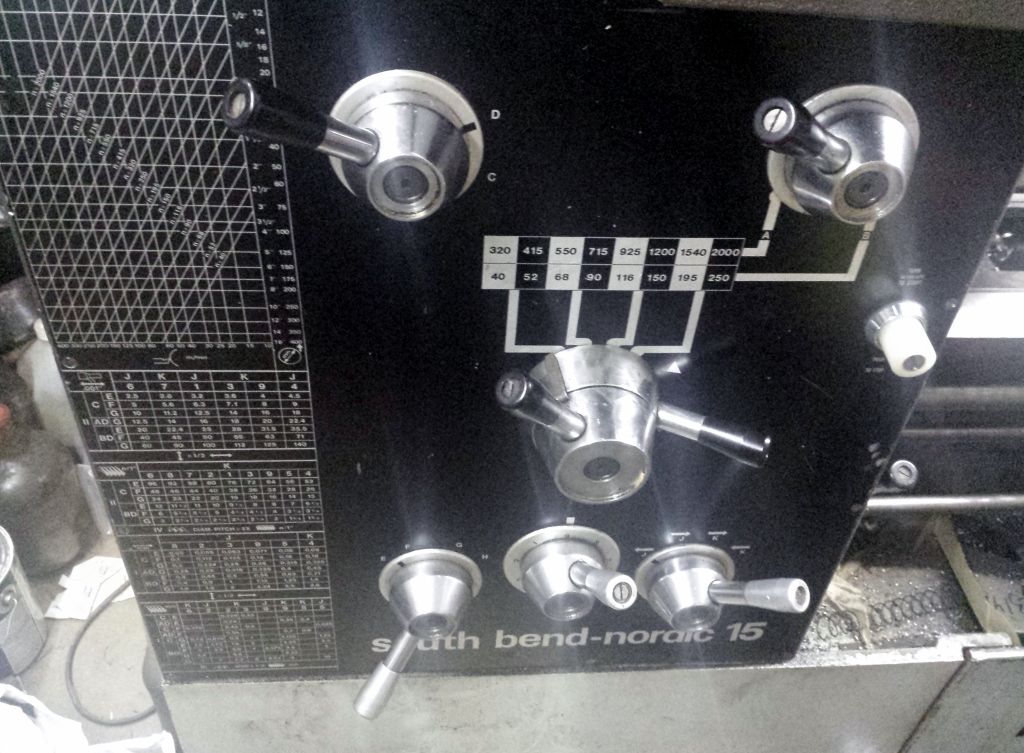 The back gears had to be swapped out for metric: 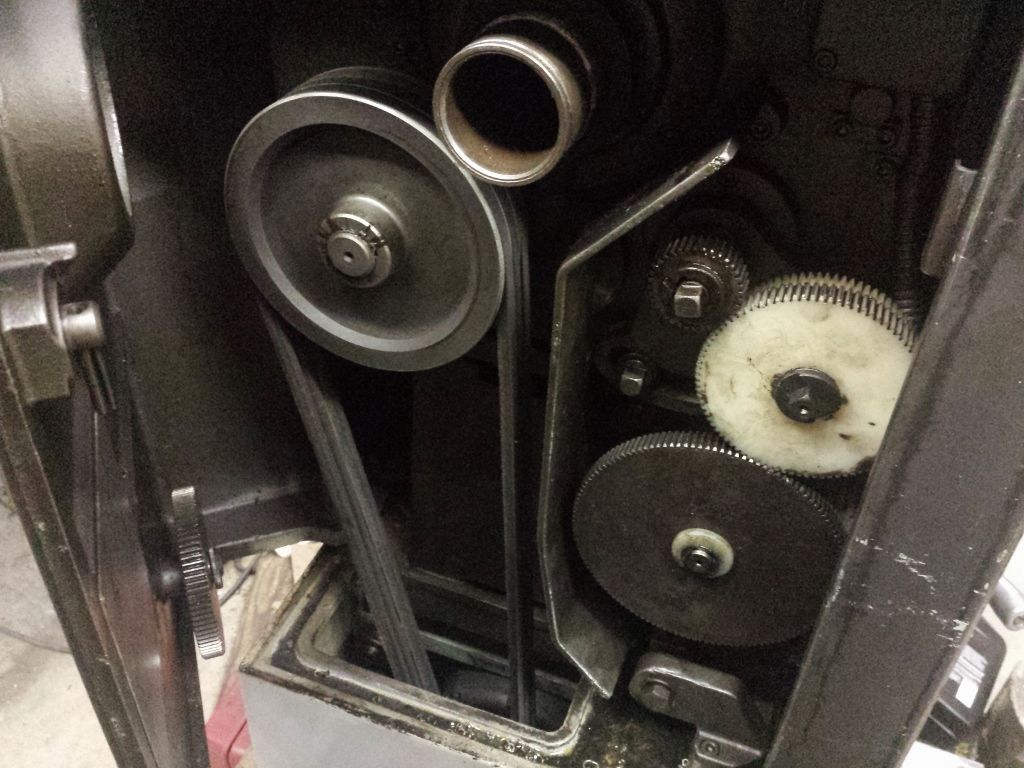 Video of the threading process. The 4-jaw chuck illustrates the size of this machine: 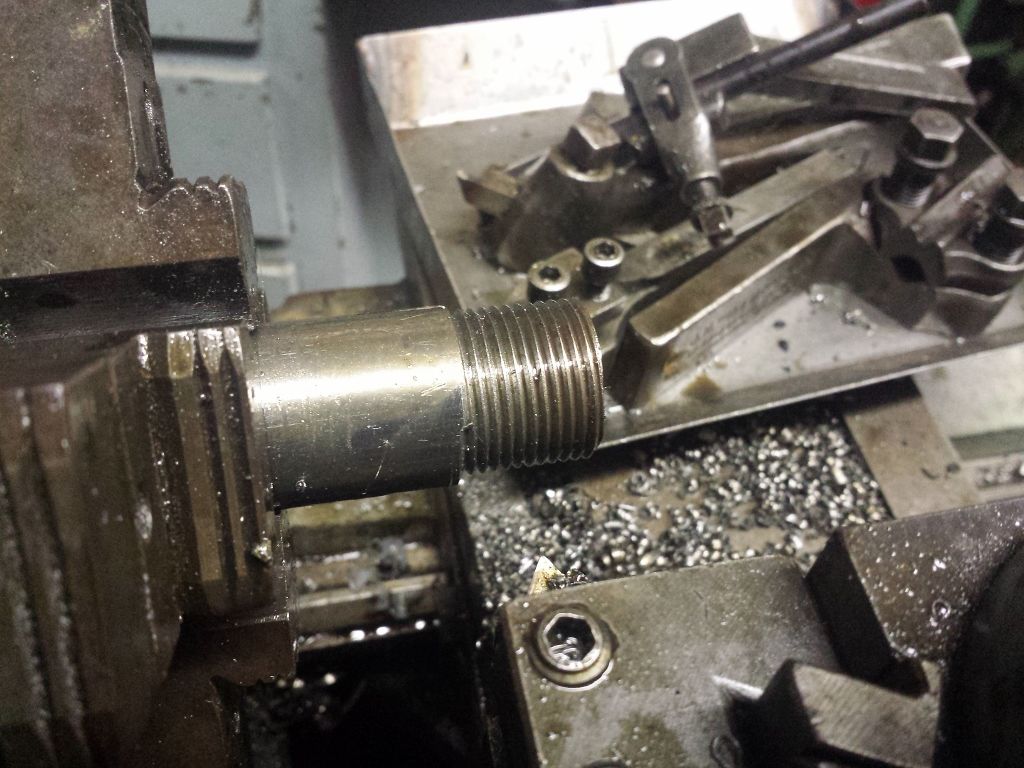 CZ 550 screwed on to the test tenon. They were snug and perfected timed.  Next weekend we’ll thread and chamber the McGowan. -Lee www.singleactions.com"Chasing perfection five shots at a time"
|
|
cmillard
.375 Atomic
 
MOLON LABE
Posts: 1,999
|
Post by cmillard on Aug 2, 2016 11:11:59 GMT -5
look forward to the results! surprised you are using a McGowan, figured you would go pac nor
|
|
|
Post by Lee Martin on Aug 4, 2016 19:40:38 GMT -5
look forward to the results! surprised you are using a McGowan, figured you would go pac nor I know someone at McGowan and they knocked it out fast. -Lee www.singleactions.com"Chasing perfection five shots at a time"
|
|
cmillard
.375 Atomic
 
MOLON LABE
Posts: 1,999
|
Post by cmillard on Aug 4, 2016 22:56:15 GMT -5
friends in high places. love it
|
|
|
Post by Lee Martin on Aug 9, 2016 19:38:27 GMT -5
Didn’t get a chance to chamber the barrel but I did cast some 800’s on Sunday. Batch one was pure linotype and lubed they’ll weigh 800 grains. Batch two will be from Lyman #2 and those’ll scale ~840. 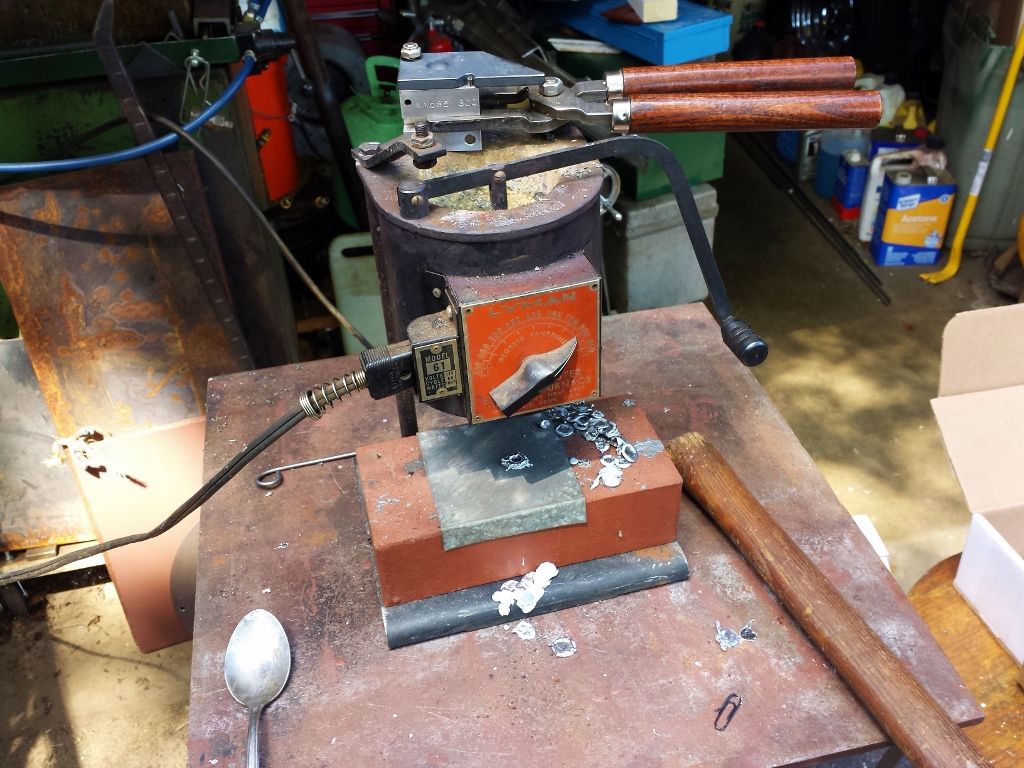 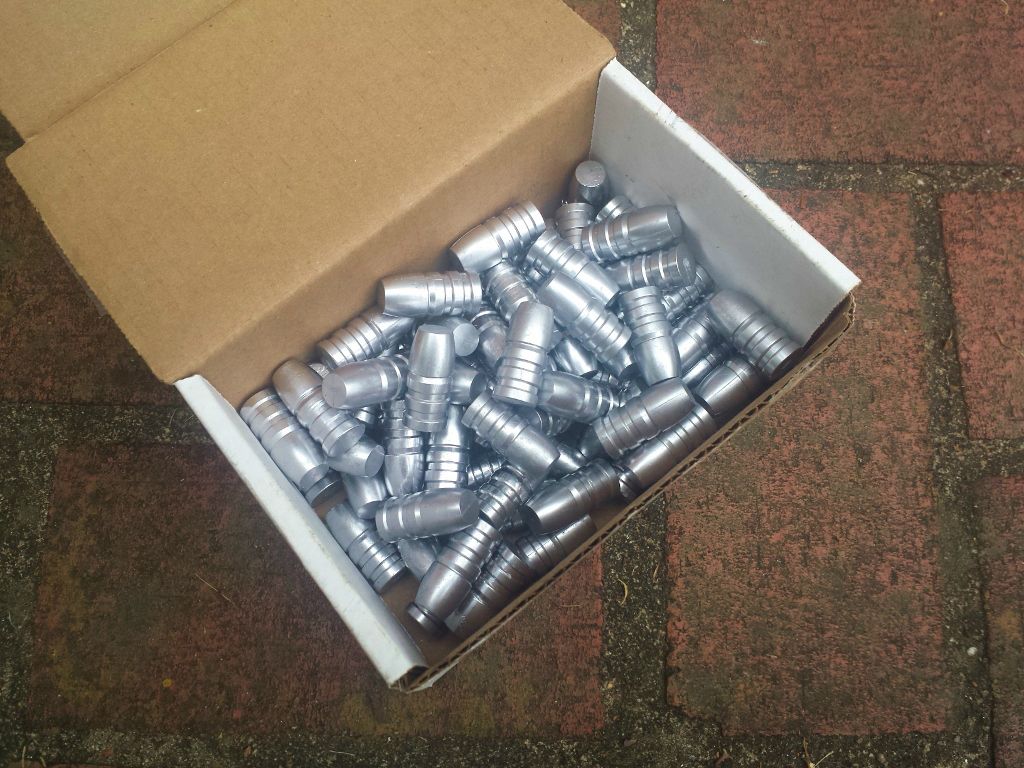 L-to-R: 585 Martin LFN (0.510”), 750 grain Woodleigh (0.585”), and our 800 grain Martin LFN (0.585”)  My Lyman 450 can’t handle a 585 lube-sizer. And I really don’t want to buy a Star for one caliber. Instead I’ll pan lube with Alox or powder coat. As cast the 800’s mic 0.588” and I’m aiming for 0.586”. We’ll machine and hone a straight die, possibly from Graph-Mo, that’ll thread into an o-press. A custom ram extension will push it through the top. -Lee www.singleactions.com"Chasing perfection one round at a time"
|
|
cj3a
.30 Stingray
Posts: 403
|
Post by cj3a on Aug 12, 2016 18:52:00 GMT -5
Lee you can get a 127 tooth gear for the southbend if you want to cut metric on it. Not that expensive.
|
|
|
Post by Lee Martin on Aug 16, 2016 19:08:38 GMT -5
Lee you can get a 127 tooth gear for the southbend if you want to cut metric on it. Not that expensive. I know. We just don't cut enough metric to buy the gear. -Lee www.singleactions.com"Chasing perfection five shots at a time"
|
|
|
Post by Lee Martin on Aug 16, 2016 19:11:40 GMT -5
The main threads have been machined. Steps summarized: The tenon is turned on a South Bend Heavy 10 lathe. Our 15” Nordic cuts metric but it’s so large we can’t center the muzzle end. The headstock is longer than the blank. The muzzle is indicated and set using a four point spider:  A chunk of the breech is turned off prior to centering: 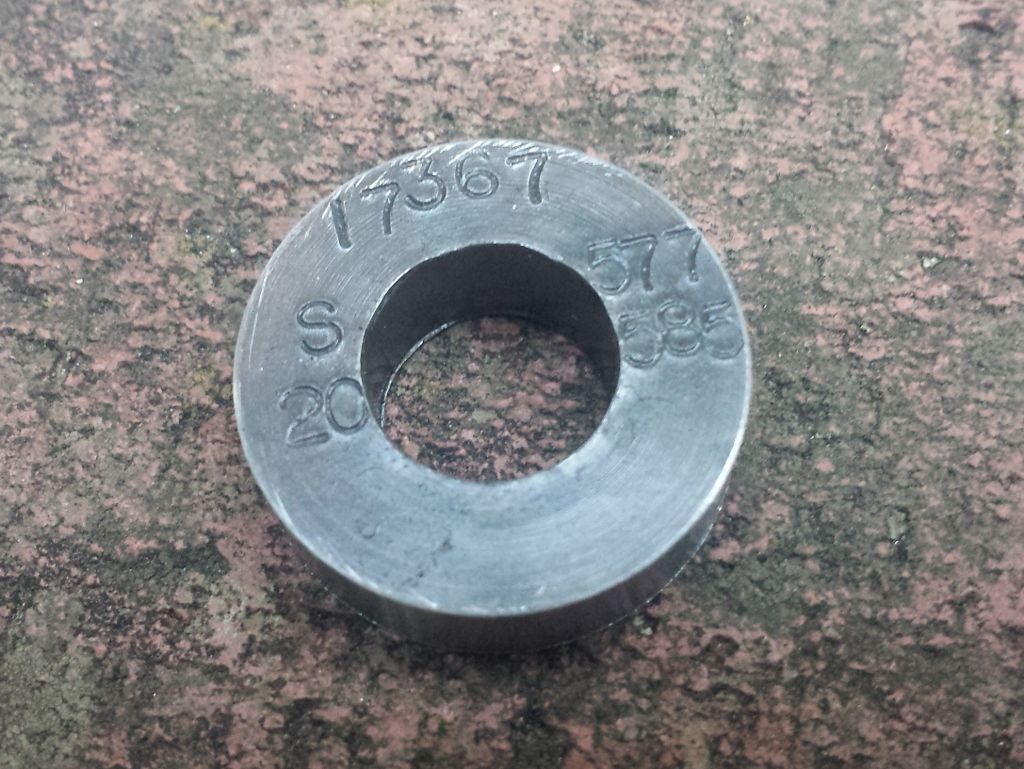 A horizontal dial test indicator is used to true all six grooves. These have 0.0005” graduations, but splitting the marks gets to 0.00025”. 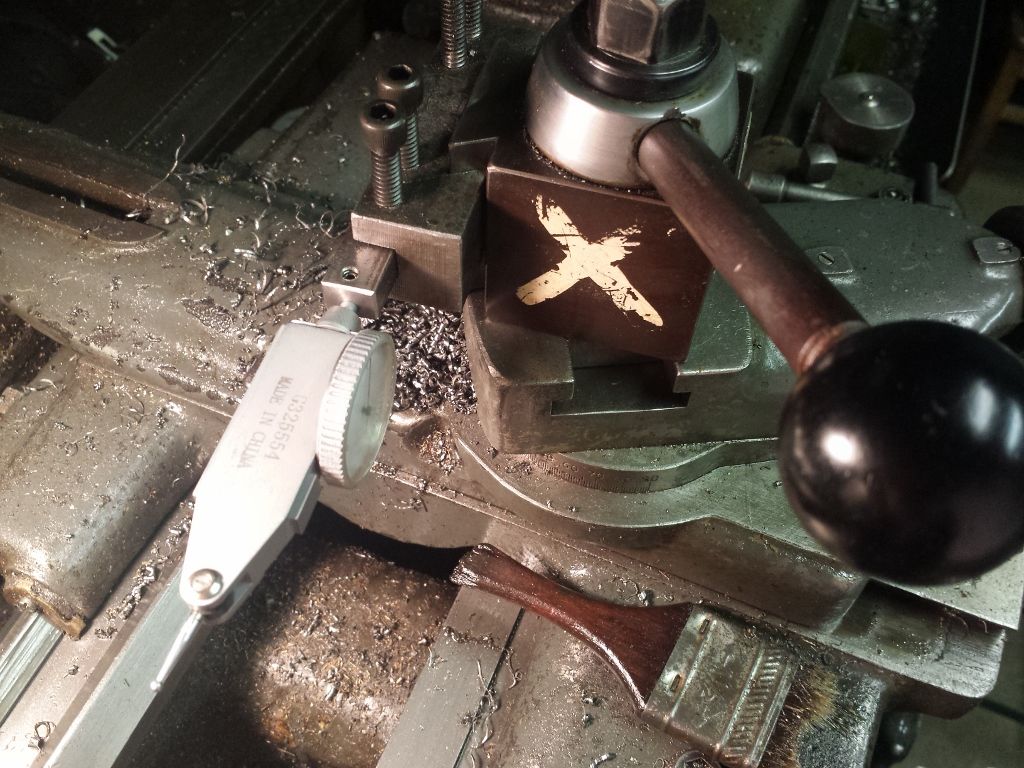 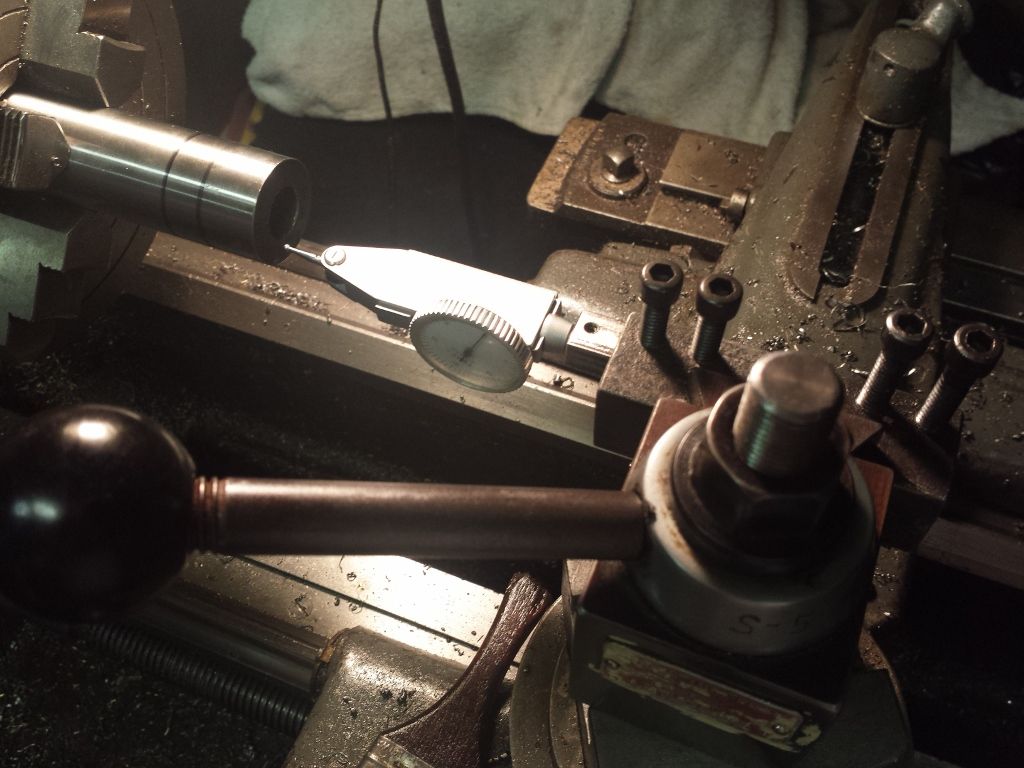 The probe is run into the rifling and the 4-jaw chuck is slowly rotated. As the finger rides over the lands and back into the grooves, the dial moves. Low spots are grooves, high measurements are lands. Once a groove is found, the dial is zeroed. Using the chuck key, the headstock is gently moved 180 degrees. Runout is noted by how far from zero that groove is relative to the opposite side. The chuck jaws are finely adjusted until both opposing grooves read 0.0000”. This procedure is repeated for the other two pairs of opposed grooves. There is no more accurate way to indicate a bore. Every barrel we do, whether it be a Ruger conversion or benchrest rifle gets this treatment. At some point I’ll illustrate the method on machining forcing cones.  The tenon is then turned. CZ 550 Magnums are 0.637” long and 1.110” in diameter. A depth stop is set on the lathe table to create the shoulder: 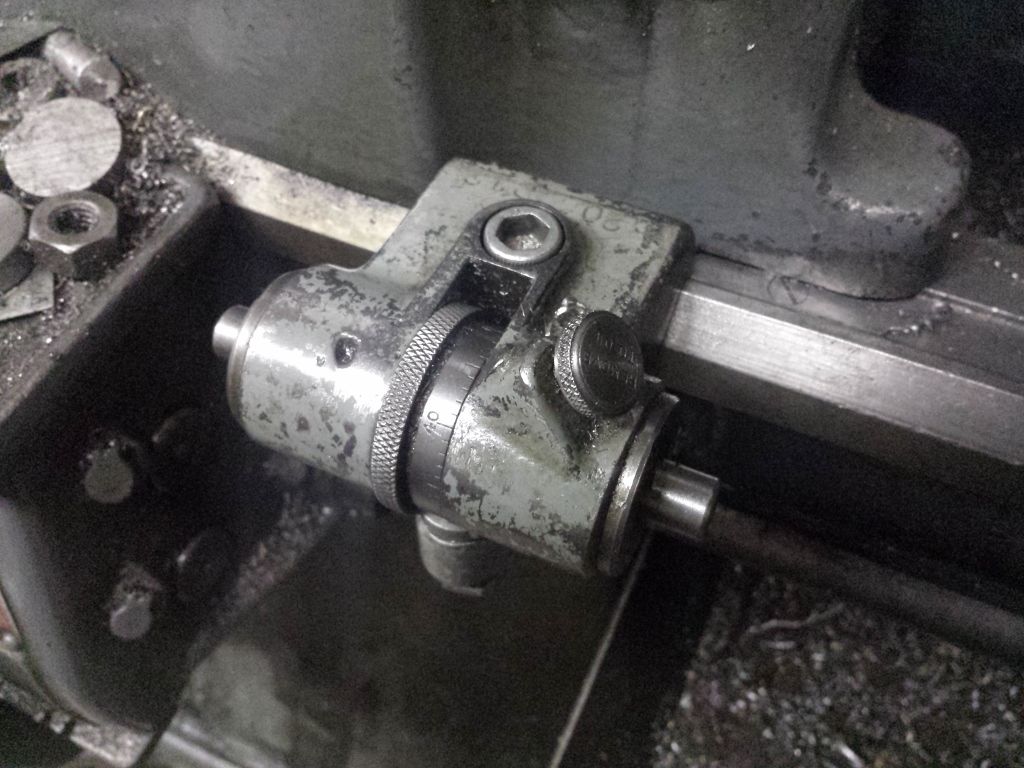 You’ll notice a relief cut is made between the shank and shoulder. This forms a stop point for the 2mm threads.  The barrel is now completely re-indicated in the Nordic for metric threading:  A dial is set on the table and zeroed for the lead edge of the tenon relief. When the dial hits zero the automatic feed is disengaged. 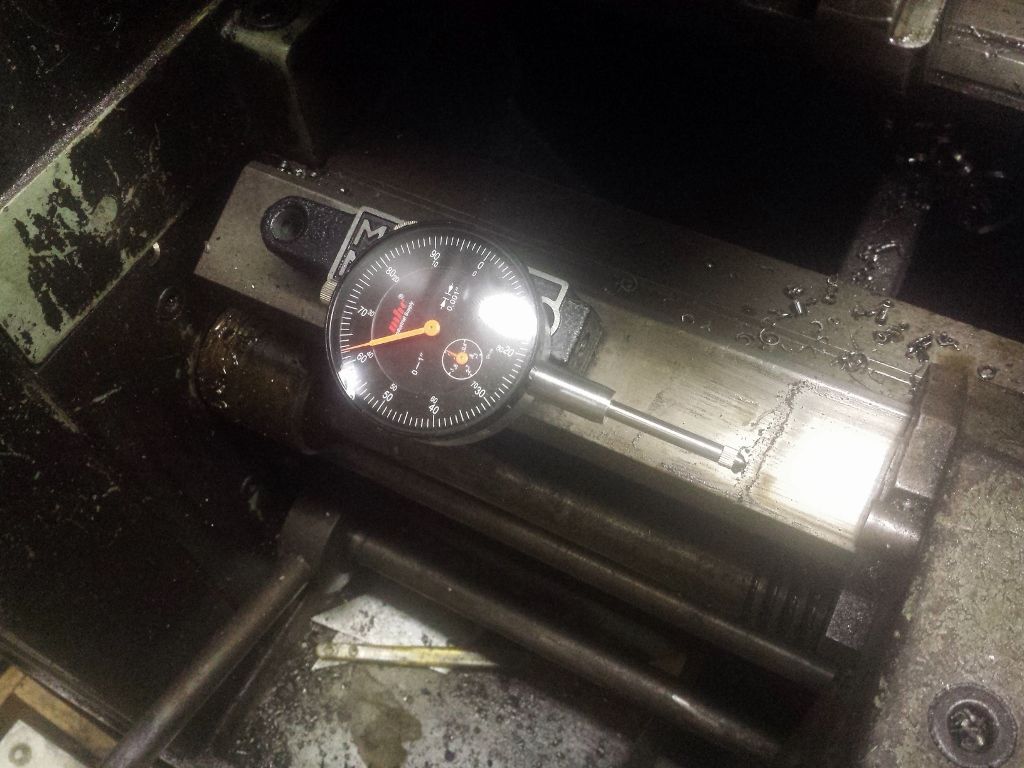 The action is tested on the tenon. Thread depth is correct when a snug fit is achieved.  The pitch diameter of a threaded object can’t be measured directly except with specialized thread micrometers. But using three wires of the same known diameter, the thread pitch can be found with a standard micrometer. This three wire method was done to validate the threads. 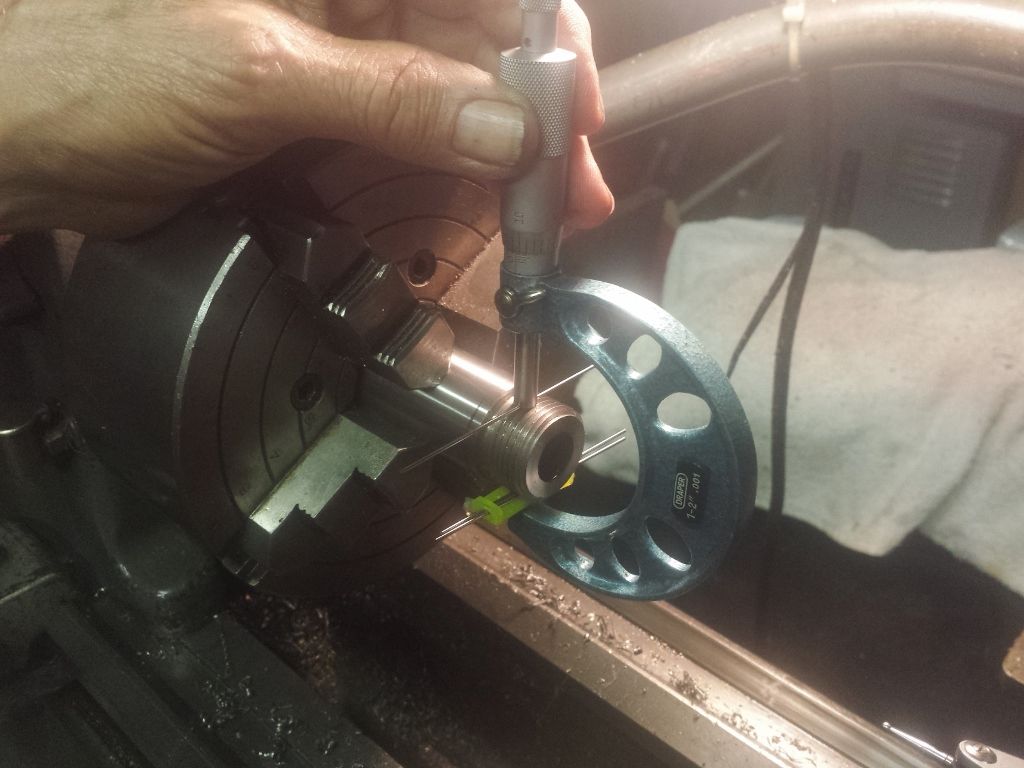 We’ll have to open the bolt face before chambering. Otherwise we can’t check headspace with the go-gauge. More to come. -Lee www.singleactions.com"Chasing perfection five shots at a time"
|
|
|
Post by Rimfire69 on Aug 17, 2016 7:03:44 GMT -5
Exellent, great pictures of the proccess, next best thing to standing there looking over your shoulder.
|
|
|
Post by Lee Martin on Aug 23, 2016 19:04:34 GMT -5
We open bolt faces in a lathe using a grinding attachment. The rear of the main body is held in a collet. The bolt head is supported with a steady rest. 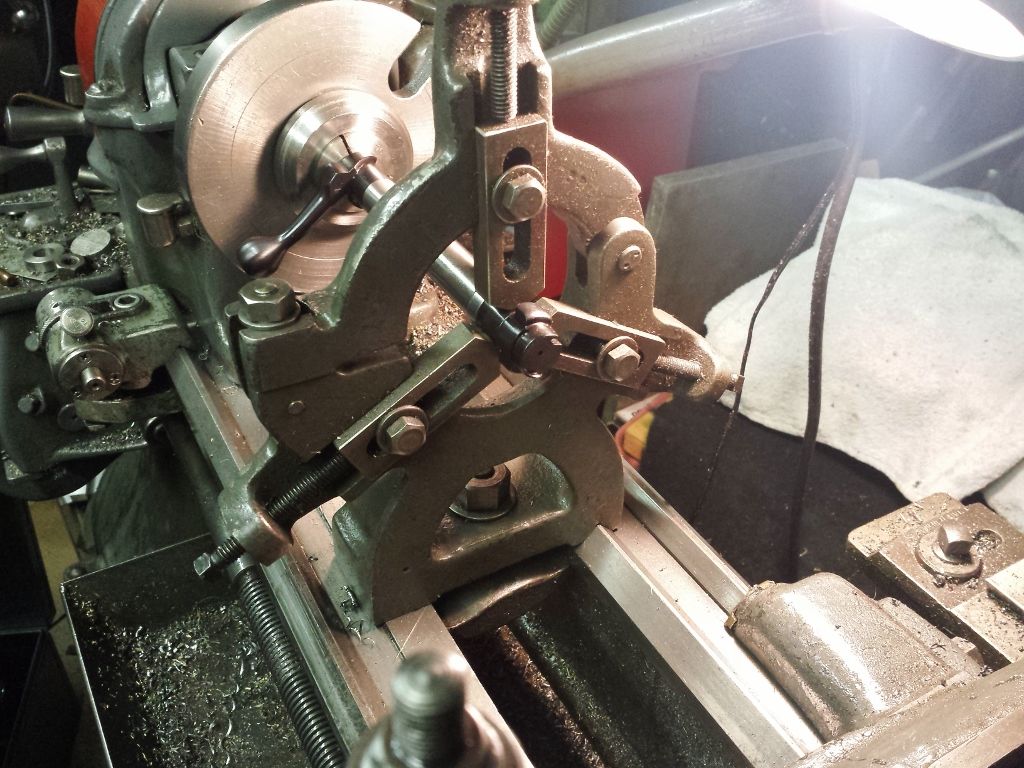 The firing pin hole is indicated with a center. 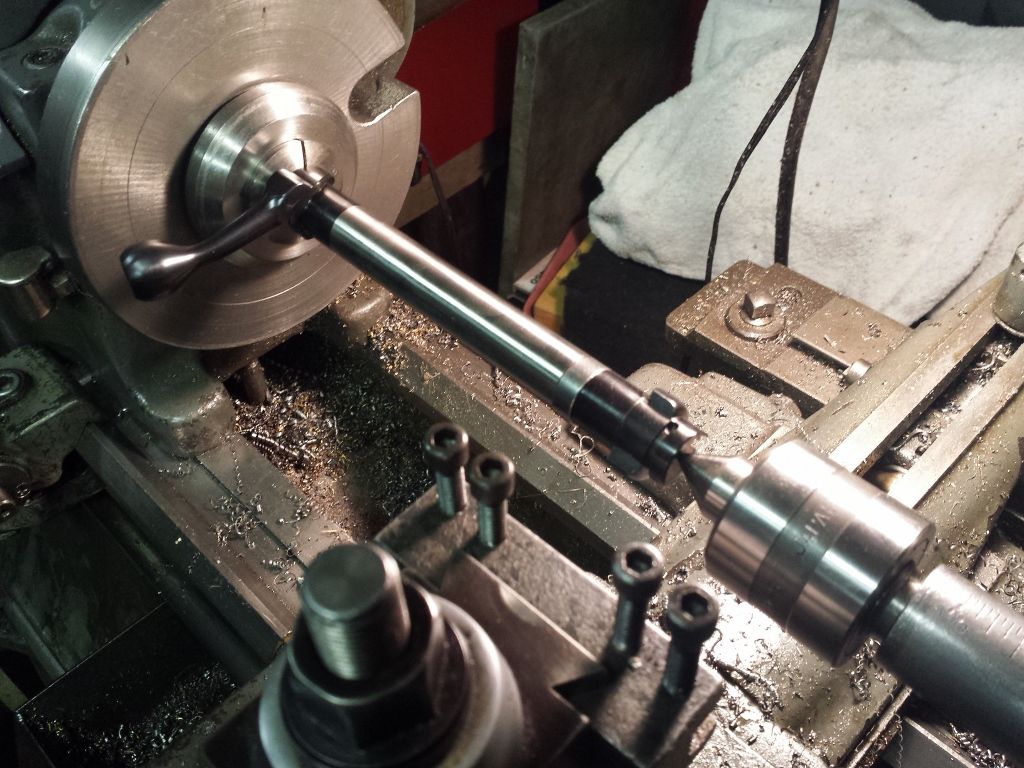 A lathe tool post grinder is anchored to the cross feed:  The grinding bit is zeroed against the bolt face, then backed off a thousandth or two: 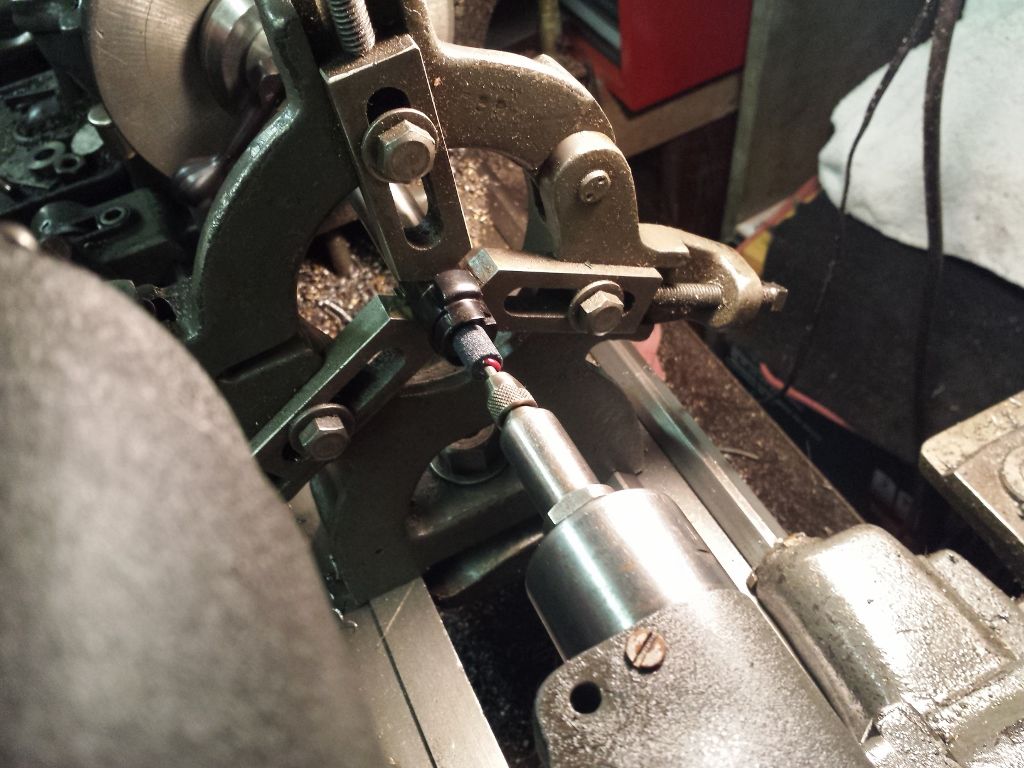 Our cross feed is slowly dialed out until it contacts the bolt lip. We took 0.005” a pass and tested a Nyati case until it fit. 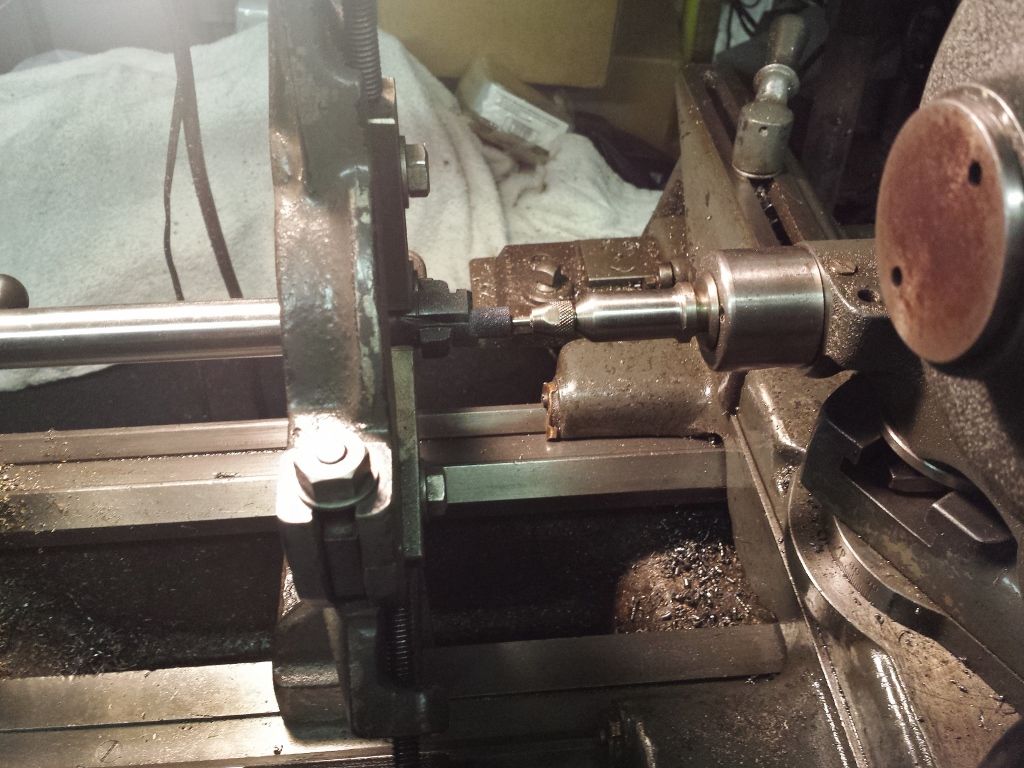 Video of this step: -Lee www.singleactions.com"Chasing perfection five shots at a time"
|
|
|
Post by Lee Martin on Aug 23, 2016 19:10:55 GMT -5
Now that the bolt is opened we can chamber the barrel. Headspace was calculated as follows: Main ring face to inner ring = 0.637” Main ring face to bolt face = 0.776” Headspace = 0.139” The reaming was uneventful but took a while. Total case length is 2.800” minus the 0.139”. 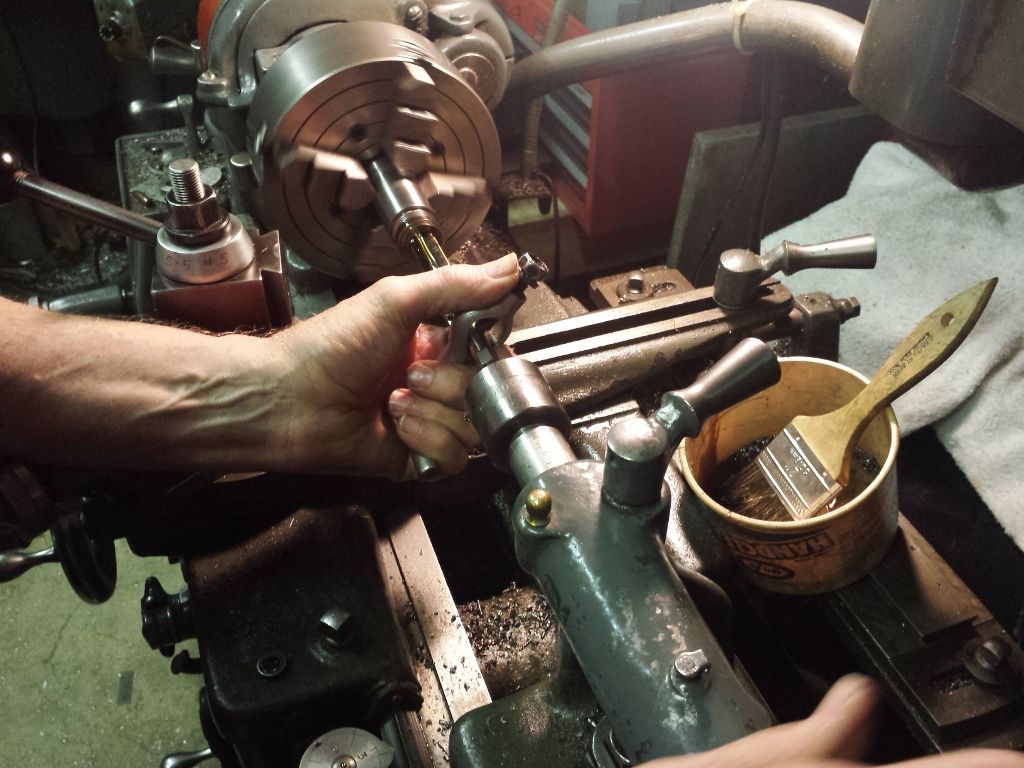 The headspace gauge was checked with a depth mic. Once 0.139” was achieved we tried the go-gauge in the action. It cycled well with just the right amount of resistance on closure. 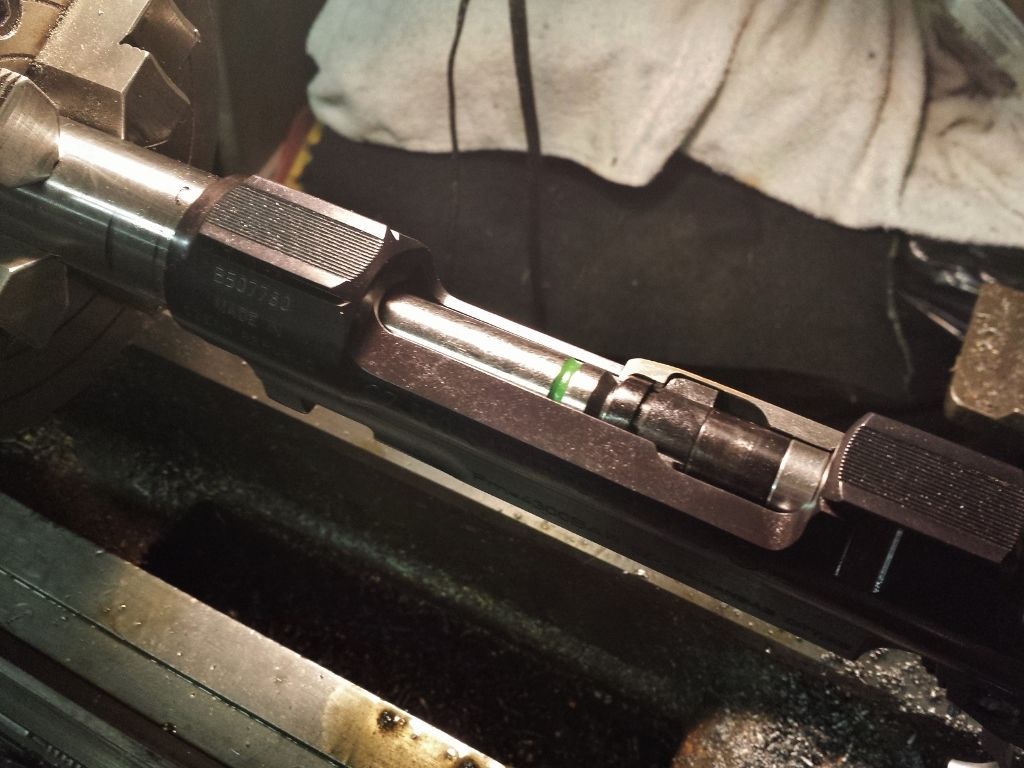 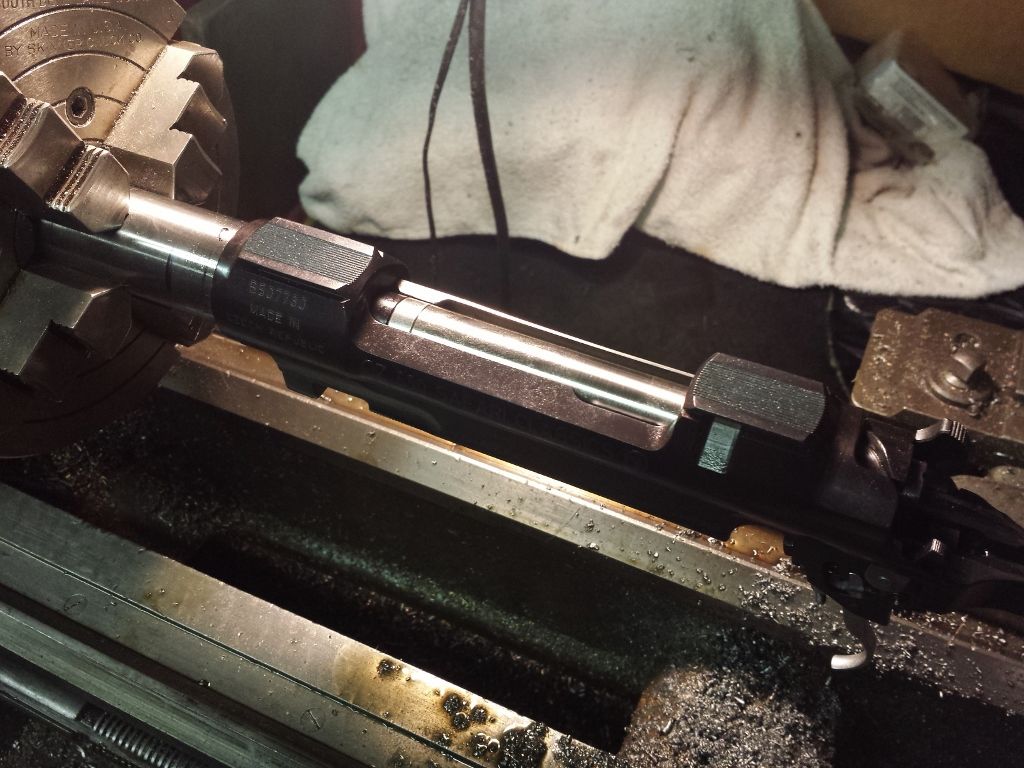 Video of the reamer in action: Next time we’ll build the muzzle brake. -Lee www.singleactions.com"Chasing perfection five shots at a time"
|
|
|
Post by Lee Martin on Aug 30, 2016 19:51:42 GMT -5
No clue of the load level: Kinda thought he was acting it up until I saw the slow motion clip. His shoulder got rung pretty good. -Lee www.singleactions.com"Chasing perfection five shots at a time"
|
|
|
Post by whiterabbit on Aug 30, 2016 20:06:25 GMT -5
I get hit harder by my wells. Being 6'3" and 150 does not help. I assume yours will be MUCH softer due to the brake.
|
|
cmillard
.375 Atomic
 
MOLON LABE
Posts: 1,999
|
Post by cmillard on Aug 31, 2016 9:12:40 GMT -5
i think you have something to look forward to lee! I would like to see a 20 shot group;-)
|
|