|
Post by Lee Martin on Apr 3, 2014 9:17:22 GMT -5
A lot of material to cover here so I'm splitting David's submission into two parts. Like many of you, I'm eager to hear more about each point (especially Eric Unger and the Alaskan) ______________________________________________ The silhouette seesaw swayed between between Smith & Wesson and Ruger into 1979, when Ruger introduced what soon would earn the the name "Silhouette Super." The S410N .44 with 10-1/2" barrel brought the duel to an end. 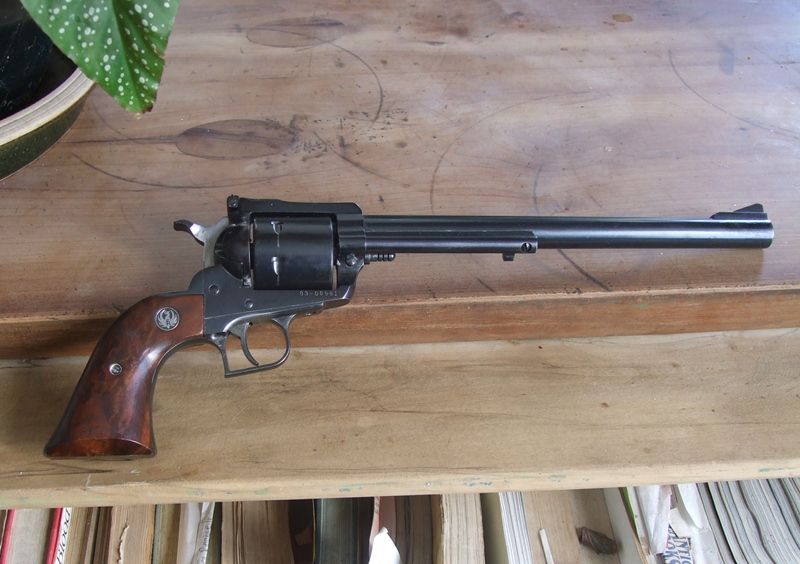 Ceramics engineer Eric Unger was brought to Sturm, Ruger in 1972 by Newport manager and metallurgist Stan Terhune. Unger holds Revolver Champion SBH, which hardware was cast under Unger's watch in Newport, New Hampshire, then machined and assembled in Southport, Connecticut. 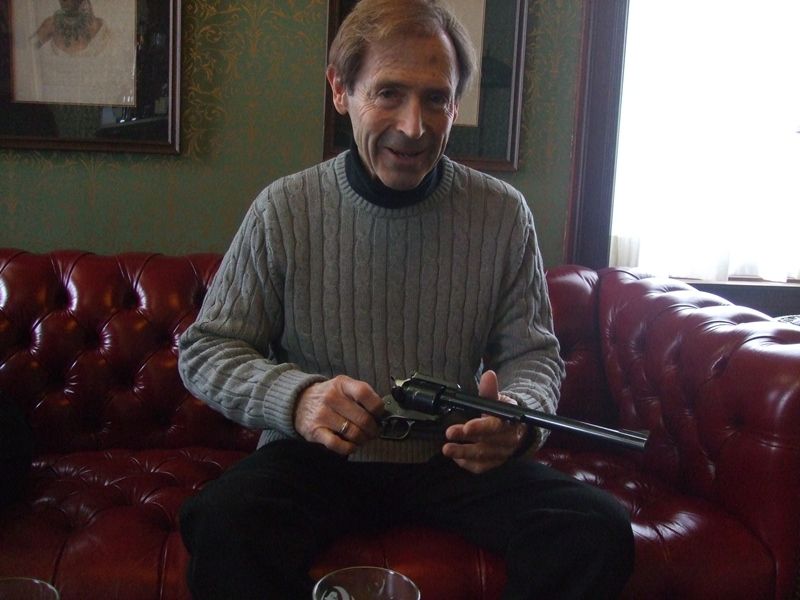 Eric Unger explains aspects of manufacturing to Terry Palumbo. Unger retired as manager of Ruger's Pine Tree Castings. Unger purified titanium casting. The Super Redhawk Alaskan was his idea----immediately embraced by Bill Ruger, Jr. Unger built a titanium Alaskan .480 Ruger, which exists in prototype only. 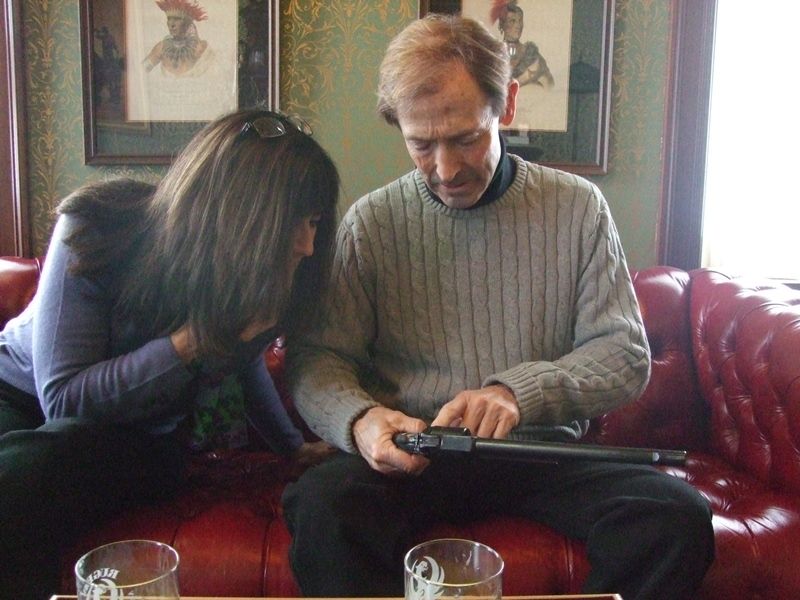 Absolute minimum wear signature, considering mileage on this revolver. No other revolver in the world would hold up any better. 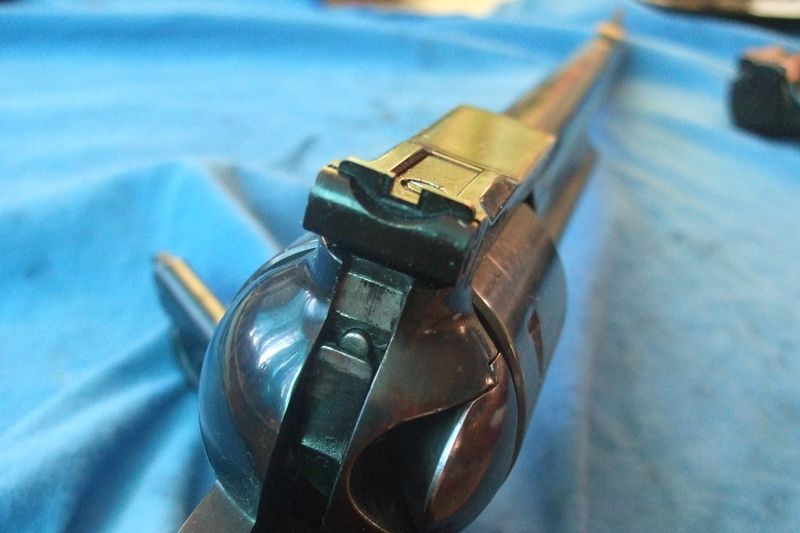 Short 11-degree forcing cone. Barrel set back to eliminate erosion immediately prior to the first International Revolver Championship. Minor erosion since then. 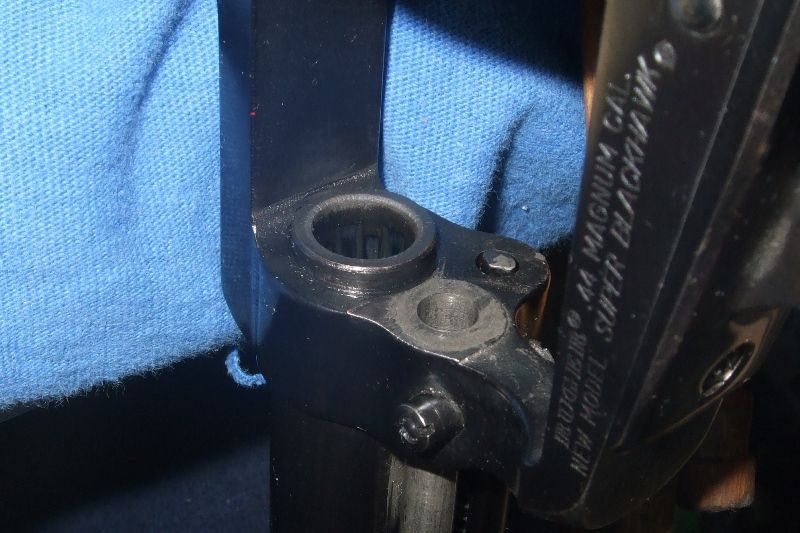 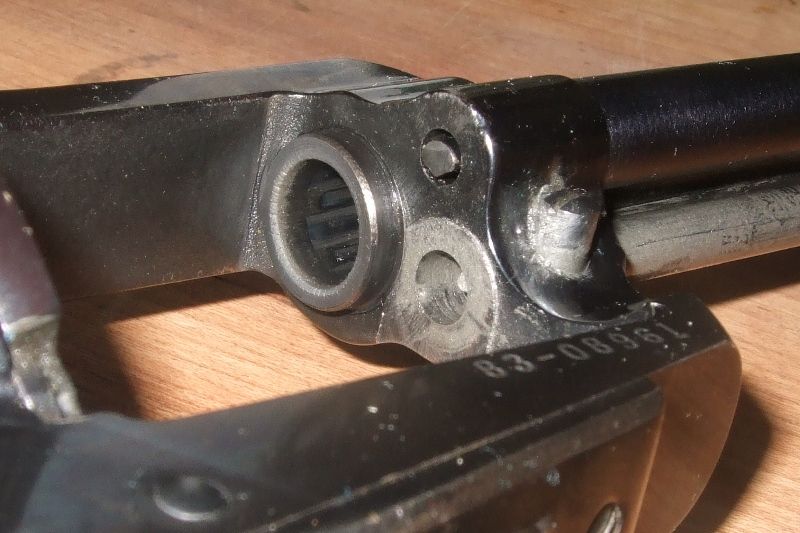 Very low wear signature attributable to cushioning effect of proper lubrication. 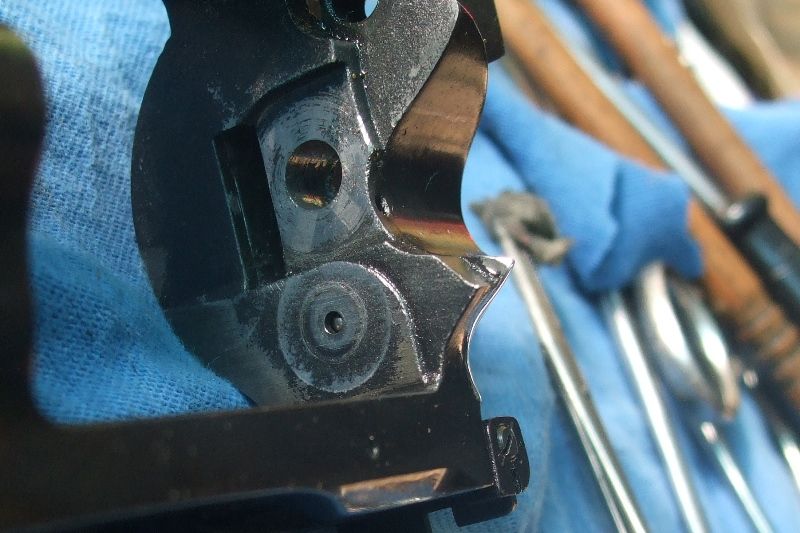 Original 8-clicks per revolution rear sight elevation screw, while a bit coarse, provides consistent and generally uniform adjustments. As with all adjustable sights, should be lubricated. 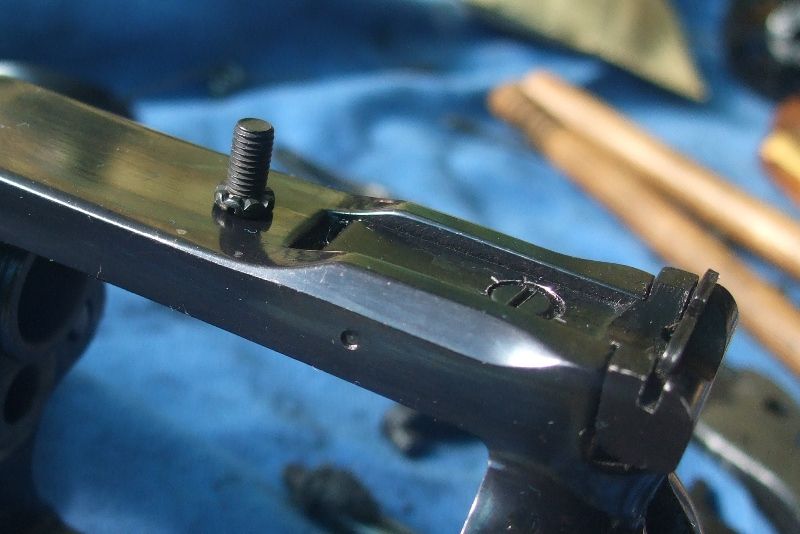 Bradshaw performed trigger jobs on all SRM prototype .357 Maximums. Mechanics would replace lockwork each time the SRM's went back to Southport. To save the trigger jobs, all of which were done at the Ruger farm in New Hampshire, David removed the lockwork at the end of each Newport test session. David later put cannibalized SRM hammer & trigger in the Silhouette Super. 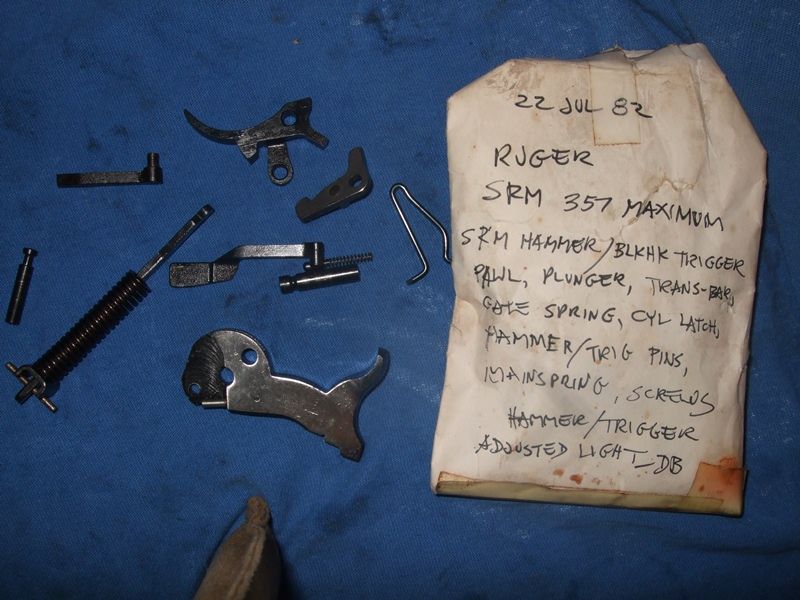 Ruger replaced cylinder at same time as setting back barrel. Cylinder gap .007-inch, without endshake. 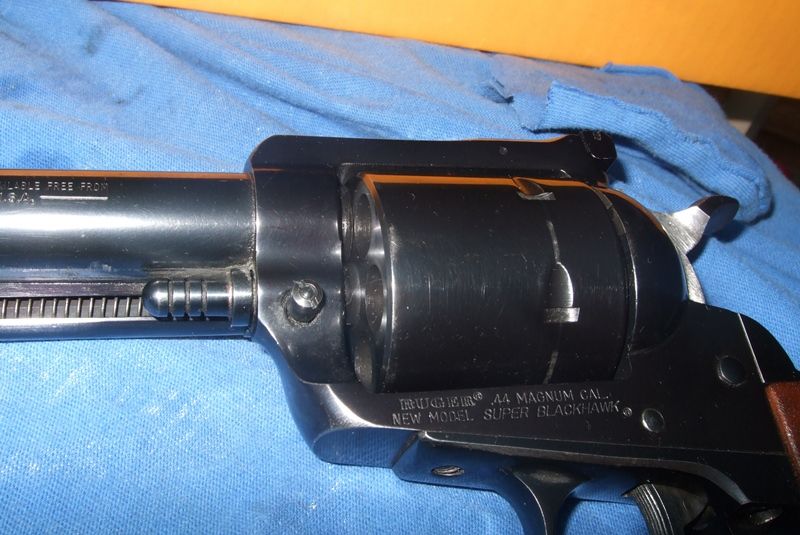 Groove diameter of broached barrel started at .428", is now .429-inch. George Wilson supplied most of Ruger barrels until hammer forging machines were installed in New Hampshire. Single action tooling was trucked from Southport to Newport 1991-92 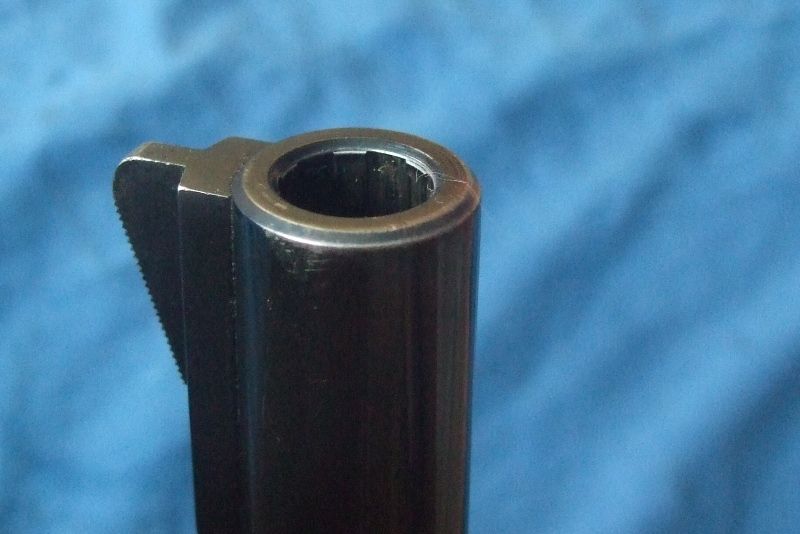 -Lee www.singleactions.com"Building carpal tunnel one round at a time"
|
|
|
Post by bradshaw on Apr 3, 2014 11:40:31 GMT -5
Investment castings for SBH, pictured here in Vol. XXXIV, made in 1979, and the Ruger 03 (2003) pictured in Vol. XXXIII, were made under the watch of Eric Unger. Production expansion envisioned by Bill Ruger, Sr., increased under Unger, and included the move into titanium. As the aerospace industry learned, titanium poses severe manufacturing challenges. Unger refined titanium casting, which requires special vacuum furnaces. The nitrogen purging used by Ruger to homogenize the pour with chrome-moly and stainless is insufficient to cleanse titanium and prevent all sorts of chemical and hardness problems.
Unger is a hiker and outdoorsman, of modest stature. While hiking, he came up with the idea of a snubnose Super Redhawk. The barrel would be the length of the SRH barrel socket. To rifle what amounts to little more than a blind hole would be costly and fraught with quality challenges. Thus, a rifled sleeve with abuttment shoulder is screwed into the cylinder frame and flushed off. After numerous goofy names were suggested and dropped, the appellation "Alaskan" popped up, and stuck. Unger wanted lighter, and an Alaskan was built----with titanium cylinder frame, crane, and trigger guard module. Lockwork remained standard SRH stainless. The Unger titanium Alaskan is chambered for the .480 Ruger.
Projected cost of production, with corresponding suggested retail, probably did more to table production than the revolver's stout recoil.
Eric Unger's work brought other manufacturers to Ruger, which includes receivers and parts for many guns which don't wear the Ruger name. Cylinder frames from Pine Tree are seen on Freedom Arms and the Magnum Research BFR. David Bradshaw
|
|
|
Post by bradshaw on Apr 3, 2014 12:35:44 GMT -5
As with all Southport revolvers, the 10-1/2-inch barrel on this SBH was made by the George Wilson Company in Connecticut. It is gun broach rifled the standard .44 1:20" twist. As received in 1979, the barrel immediately copper-streaked. Shooting only jacketed, many Hornady, mostly Sierra. Following many strokes of J-B Bore Paste----on a cotton flannel patch wrapped tightly over a 3/8-inch hardwood dowel----the copper fouling virtually disappeared.
The Sierra 240 JHC grouped 5-6" @ 200 meters. The revolver never had a scope on it. The last four shots fired prior to taking the line at the Internationals----recall sight depressed two clicks----took four turkeys in the leg, 150 meters. This shooting was done at Dick Riley's range in Hooksett, New Hampshire, after Ruger set back the barrel to eliminate forcing cone erosion. To my horror the cylinder was replaced at the same time the barrel was set back. Fortunately, the new cylinder did not destroy accuracy.
While enjoying its retirement, this Silhouette Super got to breathe the air this winter, and punch tin and rocks out yonder, down to 20 and 30-below ZERO. David Bradshaw
|
|
lah
.30 Stingray
Posts: 432
|
Post by lah on Apr 3, 2014 12:37:06 GMT -5
An employee told me that Douglas shipped several 44 barrels to Ruger. Are you aware of this?
|
|
|
Post by bradshaw on Apr 3, 2014 13:20:43 GMT -5
lah.... probably wrong to say all barrels from Wilson. Factories often are tight-lipped about where their barrels come from. Heard many years ago that Ruger used Douglas barrels in .220 Swift, which accuracy the owners speak of respectfully. Do you know whether Douglas broach rifled? I associate Douglas with button rifling. Wilson produced both button and broach rifling.
Ruger .357 barrels from Wilson are 1:16 button rifled. Any new Ruger from Newport probably wears a barrel hammer forged in house. An exception would be the standard Redhawk, which barrel begins, same as traditional S&W, with a drop forging, which must then be drilled and broached. When I viewed the Redhawk setup, drop forged barrel blanks came raw from outside, with all finish work in Newport.
The Super Redhawk uses a in house hammer forged barrel, with perhaps three barrels cut from one blank. David Bradshaw
|
|
|
Post by bradshaw on Apr 3, 2014 13:32:11 GMT -5
Between a tight and a loose bore there is no choice. The tight bore wins. Years ago, at a match at Blue Trail Range in Wallingford, Connecticut, a Lyman representative told me his Super Blackhawk sported a barrel with .432-inch groove diameter. As Lyman no longer made custom molds, a standard mold dropped bullets too small for the groove. I told him to take the revolver back to Ruger. Variation in groove diameter makes for disparity in accuracy of Rugers with Wilson barrels. Ruger is not the only company suffered this disease. David Bradshaw
|
|
petep
.30 Stingray
Central Alabama
Posts: 453
|
Post by petep on Apr 3, 2014 15:02:39 GMT -5
David,noticed this statement on your great post "Very low wear signature attributable to cushioning effect of proper lubrication. " Just curious as to what you used on the recoil shield,front of cylinder bearing and the base pin.
|
|
|
Post by bradshaw on Apr 3, 2014 22:31:05 GMT -5
petep.... Anti-Seize Compound is my preference. Chassis grease will do. Motor oil takes third place. Cylinder pin and hubs. Lockwork gets oil, sometimes grease and oil. Sight, especially elevation screw, gets oil----or grease. Pawl and transfer bar get grease. Cylinder notches are not lubed. Coil springs get oil----or grease, if grease helps hold in place during assembly.
Hard North Country winter better cold weather lube, which means synthetic motor oil, sometimes the lightest.
I have used Anti-Seize and chassis grease on S&W ratchet and hub; oil everywhere else.
Oil adjustable sights, especially the elevation screw. David Bradshaw
|
|
cmillard
.375 Atomic
 
MOLON LABE
Posts: 1,996
|
Post by cmillard on Apr 3, 2014 23:27:43 GMT -5
I had a 10.5 inch superblackhawk that was super accurate with a heavy dose of h-110 and 340 rimrocks. I wish I would not have sold that single action!
|
|
petep
.30 Stingray
Central Alabama
Posts: 453
|
Post by petep on Apr 4, 2014 3:40:42 GMT -5
Thank you for the lube answer.I noticed in the assembly photos you seem to get a buildup of something on your hands,I thought it might be moly-Kote.
|
|
|
Post by bradshaw on Apr 4, 2014 8:48:45 GMT -5
cmillard.... those guns were made before Gorilla Monsoon got into the barrel fitting department, or someone ignorant of BARREL THREAD TIMING eliminated a step critical to barrel installation; a step very well understood by revolver makers and rifle makers well back in the eighteen hundreds. Now, when a member posts pictures of a super accurate revolver, we may assume excellent thread timing on that revolver. It is the easiest thing in the world to cure----during manufacture.
petep.... silver on my hands is Anti-Seize Compound. One of my High Power Rifle instructors, maestro hard holder Sam Burkehalter, got me away from Lubripate white petroleum grease on the M1 Garand. Said Lubriplate gets all gummy in the rain. Handed me a can of transparent orange synthetic grease. "Use this on the M1," he said. Ruger
If observation is worth anything, I found Anti-Seize to work especially well on the cylinder hubs of the S&W M-629 and Redhawk stainless revolvers. I use it on the Freedom Arms as well, although the closer fit of cylinder/cylinder favors for oil. On a close fit 1911 such as the Les Baer, I lean toward synthetic motor oil, sometimes automatic transmission fluid in winter, and the guns are dead reliable at deep freeze.
Warren Center lang ago cautioned against lubricating the locking bolt of his T/C Contender. Note under recoil the frame wants to pull away from the spring loaded bolt, much as a magnum S&W recoils away from the spring loaded cylinder pin. Bolt actions should be lubricated at cocking cam and locking lugs. Lubrication is critical to prevent galling on some models, especially the Remington M700 and XP-100 and all stainless bolt actions. David Bradshaw
|
|
lah
.30 Stingray
Posts: 432
|
Post by lah on Apr 4, 2014 11:51:22 GMT -5
Do you know whether Douglas broach rifled? I associate Douglas with button rifling. I can't say 100% but I've personally known of only of button rifling.
|
|
cmillard
.375 Atomic
 
MOLON LABE
Posts: 1,996
|
Post by cmillard on Apr 4, 2014 14:06:12 GMT -5
button.
|
|
|
Post by bradshaw on Aug 7, 2023 10:53:15 GMT -5
Photo #8----ELEVATION SCREW----original 8-click per rev screw with consistent detents for predictable elevation changes, critical in top IHMSA competition. In attempt at smaller increments, Ruger ireplaced 8-click with 16-click screw. Result, less consistent elevation adjustment. Finer is better only with consistency. Some, not all, 16-click screws work as intended.
I lubricate micro-adjustments on all iron sight guns. When when sights are counted up & down multiple times a week, grease or oil prevents premature wear. Bo-Mar told me years ago that their elevation screw is meant to wear out before the sight. My answer to the Bo-Mar challenge----grease!
With the RW2dogs Sight now in production, it’s time to repeat the obvious: lubricate elevation & windage screws on Ruger base sights. David Bradshaw
|
|
James
.30 Stingray
Posts: 497
|
Post by James on Aug 7, 2023 13:25:32 GMT -5
What "don`t" you know about Ruger Dave???  Interesting how the Alaskan concept came about...................
|
|